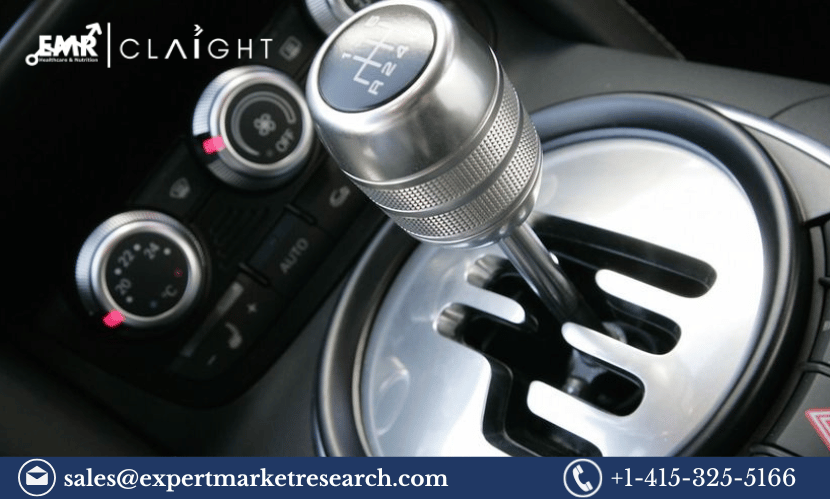
Automotive shifters, integral components in vehicles that enable drivers to change gears, have become increasingly sophisticated, with advancements in design, materials, and functionality. These systems, used in both manual and automatic transmissions, are essential for vehicle performance, safety, and driver comfort. With the growing demand for both conventional and electric vehicles, the automotive shifter market has expanded rapidly. Setting up a manufacturing plant for automotive shifters presents an exciting opportunity, as manufacturers seek to meet the evolving needs of the automotive industry. This report outlines the key steps involved in establishing a manufacturing plant for automotive shifters, including raw material sourcing, production techniques, equipment requirements, and market insights.
Overview of Automotive Shifters
An automotive shifter is a mechanism in a vehicle that allows the driver to change gears, either manually or automatically. In manual transmission vehicles, the shifter is typically operated by the driver, while in automatic transmission vehicles, it often operates with minimal driver intervention. Shifters have evolved from basic lever mechanisms to more advanced designs, including electronic, push-button, and rotary shifters. These innovations offer greater convenience, comfort, and precision.
The materials used in automotive shifters are typically selected for their durability, strength, and ability to withstand constant use and temperature fluctuations. Common materials include metal alloys, plastics, and composite materials. The design of the shifter must also take into account safety, ergonomics, and ease of use, as it is a critical interface between the driver and the vehicleโs transmission system.
The market for automotive shifters has grown significantly in recent years, driven by advancements in vehicle technology, increased vehicle production, and the rising demand for electric vehicles (EVs), which often feature different transmission systems. With innovations in automated manual transmissions (AMT) and continuously variable transmissions (CVT), automotive shifters continue to evolve in response to new consumer preferences and market demands.
Get a Free Sample Report with Table of Contents@ https://www.expertmarketresearch.com/prefeasibility-reports/automotive-shifter-manufacturing-plant-project-report/requestsample
Key Considerations for Setting Up the Manufacturing Plant
Establishing a manufacturing plant for automotive shifters requires strategic planning in areas such as sourcing materials, selecting appropriate equipment, meeting regulatory standards, and managing production efficiency. Below are the essential considerations for setting up such a plant.
1. Location and Site Selection
Choosing the right location for the manufacturing plant is critical for operational success. Important factors to consider include:
- Proximity to Automotive OEMs: Original Equipment Manufacturers (OEMs) are the primary customers for automotive shifters. Therefore, locating the plant near major automotive manufacturing hubs or OEMs can reduce logistics costs and improve production timelines.
- Access to Skilled Labor: The manufacturing process for automotive shifters requires precision and specialized knowledge, particularly in areas such as metalworking, assembly, and electronics integration. Selecting a location with access to a skilled workforce ensures the production process runs smoothly.
- Utility Access: The plant will need reliable access to utilities such as electricity, water, and waste management services. The availability of high-quality infrastructure is essential for the operation of automated machinery and efficient manufacturing processes.
- Logistics and Distribution: The plant should be strategically located near major transportation routes to ensure timely delivery of raw materials and distribution of finished products to customers. Proximity to ports, highways, and railways can significantly reduce transportation costs.
Choosing the right location helps minimize operational costs while ensuring the plantโs long-term success.
2. Raw Materials and Procurement
The raw materials used in automotive shifters are critical to the performance, durability, and aesthetics of the product. Key materials include:
- Metal Alloys: Metals such as stainless steel, aluminum, and zinc alloys are commonly used in the construction of shifter components due to their strength and resistance to wear and corrosion.
- Plastics and Composites: These materials are used in various parts of the shifter, including the housing and internal components. Plastics such as ABS (Acrylonitrile Butadiene Styrene) and polycarbonate are often selected for their durability, impact resistance, and moldability.
- Electronic Components: In modern automotive shifters, electronic components such as sensors, actuators, and circuit boards are often integrated to enhance performance and functionality.
- Lubricants and Sealants: These are used in the assembly process to ensure smooth operation and protect moving parts from wear and corrosion.
- Packaging Materials: The finished automotive shifters must be packaged securely for shipment to automotive manufacturers or distribution networks. Packaging materials should be durable, cost-effective, and protective.
Securing a reliable supply chain for these materials is essential to avoid delays and maintain production schedules.
3. Manufacturing Process
The production of automotive shifters involves several key stages, from material preparation to assembly and quality control. The main stages include:
- Material Preparation: Raw materials, including metals, plastics, and electronic components, are prepared by cutting, molding, and shaping them into the required dimensions for the shifter components.
- Component Manufacturing: Various parts of the automotive shifter are produced, including metal brackets, levers, housings, and electronic components. This stage often involves precision machining, casting, and injection molding to create the necessary components.
- Assembly: Once the components are manufactured, they are assembled into the final product. This may involve mechanical assembly, soldering electronic components, and integrating wiring or sensors into the shifter unit.
- Testing: The assembled shifters undergo various tests to ensure functionality, durability, and safety. These tests may include load-bearing tests, ergonomic assessments, and electronic testing to ensure proper integration with the vehicleโs transmission system.
- Finishing: The final product is cleaned, polished, and painted or coated as necessary to provide a finished look and protect the shifter from environmental factors such as moisture and corrosion.
- Packaging: The finished shifters are packaged securely to prevent damage during transportation. Packaging must also include appropriate labeling and handling instructions to ensure safe delivery to customers.
Each stage of the production process must be carefully monitored to ensure product quality and efficiency.
4. Quality Control
Quality control is essential in the manufacturing of automotive shifters to ensure that the final product meets safety, durability, and performance standards. Key quality control measures include:
- Material Inspection: Raw materials should be inspected for defects, impurities, and conformity to specifications before they are used in production. This helps prevent quality issues later in the manufacturing process.
- Component Testing: Parts such as metal brackets, levers, and electronic components should undergo rigorous testing to ensure that they meet required performance standards. This includes testing for strength, resistance to wear, and compatibility with other vehicle components.
- Assembly Checks: During the assembly process, components should be checked for proper alignment, secure connections, and correct assembly procedures.
- Functional Testing: The completed shifter is tested for its functionality, including smooth operation, proper gear shifting, and electronic integration with the vehicleโs transmission system.
- Packaging Inspection: After assembly and testing, the finished products should be inspected for any cosmetic defects, correct labeling, and secure packaging to ensure they are ready for distribution.
A thorough quality control process ensures that each batch of automotive shifters meets customer expectations and industry standards.
5. Regulatory Compliance
Manufacturers of automotive shifters must comply with a variety of regulations related to product safety, environmental impact, and quality standards. Key regulatory considerations include:
- Safety Standards: Automotive shifters must comply with safety regulations to ensure they function properly and do not pose a hazard to drivers. These regulations are often set by automotive regulatory bodies such as the National Highway Traffic Safety Administration (NHTSA) in the United States.
- Environmental Standards: As automotive manufacturers increasingly focus on sustainability, shifter manufacturers must comply with environmental regulations regarding waste management, emissions, and the use of eco-friendly materials.
- Industry Certifications: Depending on the region, manufacturers may need to obtain industry-specific certifications, such as ISO 9001 for quality management or ISO 14001 for environmental management.
Compliance with these regulations ensures that the product is safe for use, meets industry standards, and can be legally sold in various markets.
Equipment and Technology
The production of automotive shifters requires advanced machinery and technology to ensure precision, efficiency, and product consistency. Key equipment includes:
- CNC Machines: Computer Numerical Control (CNC) machines are used for precision machining of metal components, ensuring that parts such as levers, brackets, and other structural elements are manufactured to exact specifications.
- Injection Molding Machines: Used to mold plastic components such as housing, buttons, and covers. These machines allow for high-volume production of complex shapes with minimal waste.
- Welding and Assembly Stations: Welding machines are used to join metal components, while assembly stations ensure that the different parts are securely connected and tested for proper functionality.
- Electronic Testing Equipment: For shifters that incorporate electronic components, such as sensors or actuators, specialized testing equipment ensures that these parts function properly and integrate seamlessly with the vehicleโs transmission system.
- Packaging Machines: Automated packaging machines are used to ensure that the finished automotive shifters are securely packaged for shipment.
Investing in state-of-the-art equipment improves manufacturing efficiency, product consistency, and safety.
Workforce and Training
A skilled workforce is essential for the smooth operation of the manufacturing plant. Key roles include:
- Production Operators: Responsible for operating machinery, assembling components, and ensuring that products meet quality standards.
- Quality Control Technicians: To monitor the production process, inspect raw materials and finished products, and conduct tests to ensure compliance with safety and performance standards.
- Machine Operators: To operate and maintain the CNC machines, molding equipment, and other specialized machinery.
- Safety Officers: To ensure that safety protocols are followed and that the plant operates in compliance with regulatory standards.
Regular training programs are essential to keep employees updated on new technologies, safety standards, and manufacturing techniques.
Packaging and Distribution
Packaging and distribution are critical aspects of the automotive shifter manufacturing process. Key considerations include:
- Packaging Materials: The packaging must protect the shifter from damage during transportation. Materials should be durable yet lightweight, and eco-friendly packaging is becoming a key consideration for many customers.
- Labeling: Labels should include product specifications, safety warnings, and handling instructions to ensure proper storage and transportation.
- Logistics and Distribution: Establishing efficient distribution channels helps ensure that the products are delivered to OEMs or retailers on time and in good condition.
Environmental and Safety Aspects
Sustainability and safety should be central to the production process. Key initiatives include:
- Waste Reduction: Implementing systems to minimize waste, such as recycling metal scraps and reducing plastic waste during production.
- Energy Efficiency: Using energy-efficient machinery and processes to reduce the plantโs carbon footprint.
- Worker Safety: Ensuring that workers are equipped with personal protective equipment (PPE) and that the plant adheres to all workplace safety standards.
Market Applications and Trends
Automotive shifters are used in a wide range of applications, including:
- Manual Transmission Vehicles: As the primary mechanism for shifting gears.
- Automatic Transmission Vehicles: To provide additional control over the shifting process, especially in vehicles with advanced automatic transmissions.
- Electric Vehicles (EVs): With the rise of electric vehicles, new types of shifters, such as push-button and rotary shifters, are gaining popularity due to their sleek design and space-saving qualities.
Emerging trends include:
- Shift to Electric Vehicles: Growing demand for advanced transmission systems in electric vehicles.
- Ergonomics and Design: Increasing consumer demand for comfortable and easy-to-use gear shifters.
Challenges in Manufacturing
Manufacturers of automotive shifters face several challenges, including:
- Raw Material Sourcing: Securing a consistent supply of high-quality materials for production.
- Technological Advancements: Keeping up with rapid technological changes in the automotive sector and adapting to new transmission systems.
- Regulatory Compliance: Ensuring compliance with increasingly strict environmental and safety regulations.
By addressing these challenges, manufacturers can position themselves for success in the growing automotive sector, meeting the demands for innovation and efficiency.
Leave a Reply