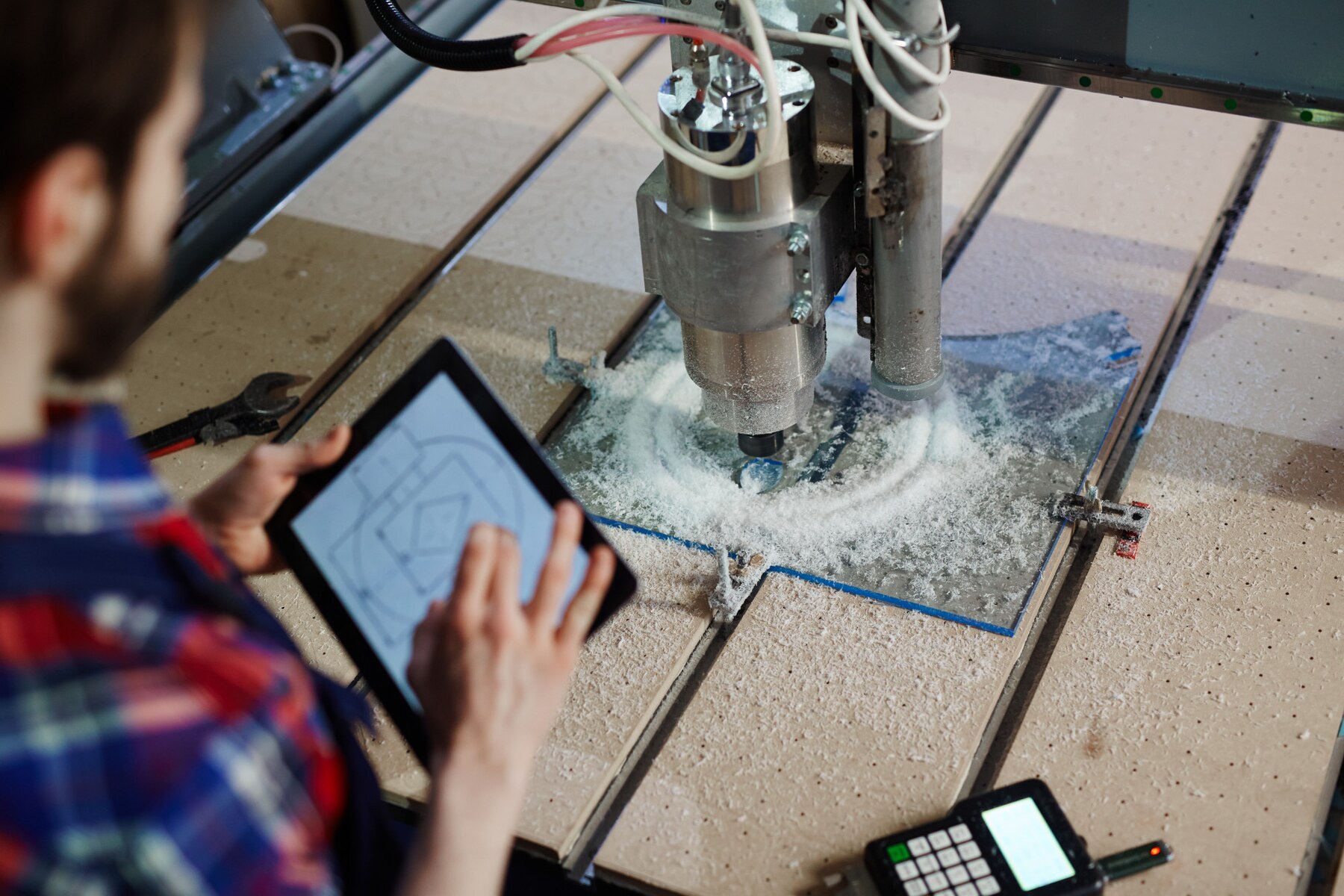
In the modern manufacturing world, businesses constantly seek methods to improve efficiency, reduce costs, and maintain high standards of quality. One technology that has revolutionized manufacturing processes across industries is CNC machining processes. Computer Numerical Control (CNC) machining offers precise, repeatable, and automated production methods, making it an ideal choice for cost-effective manufacturing. In this article, we explore how CNC machining processes can drive cost savings and improve operational efficiency for businesses of all sizes.
Understanding CNC Machining and Its Advantages
CNC machining is a manufacturing process where pre-programmed computer software dictates the movement of machinery and tools to fabricate parts and components. Unlike traditional manual machining, CNC machining is highly automated, ensuring precision and speed in production. The machines used in this process can operate continuously, reducing the need for manual intervention and thus cutting down labor costs.
The main advantage of CNC machining is its ability to produce complex parts with high precision. The technology minimizes human error, enhances repeatability, and can handle intricate designs. These capabilities make it an attractive option for industries like aerospace, automotive, medical devices, and electronics, where precision is critical. Furthermore, the automated nature of CNC machining reduces the time spent on each part, allowing for faster turnaround times and more efficient resource utilization.
Reducing Labor Costs and Increasing Efficiency
One of the most significant advantages of CNC machining processes is the reduction in labor costs. Traditional manufacturing methods often require a large workforce to oversee operations, adjust machines, and make fine adjustments during production. CNC machines, however, are automated and require minimal manual intervention once set up. As a result, businesses can reduce the number of operators and technicians needed on-site, leading to significant savings in labor costs.
Moreover, the speed and accuracy of CNC machines contribute to improved efficiency in manufacturing. Once the machine is programmed, it can work around the clock without needing rest, maintaining consistent production quality. This 24/7 capability leads to higher output in less time, making it easier for companies to meet customer demand without increasing operational costs. The high efficiency of CNC machining processes also helps manufacturers stay competitive by enabling them to reduce production costs while maintaining product quality.
Minimizing Waste and Maximizing Material Usage
In traditional manufacturing processes, excess material is often wasted during the machining and fabrication phases. However, CNC machining processes are designed to be more material-efficient. Since the machines are controlled by computer programs, they can precisely cut and shape materials according to the exact specifications, minimizing waste. Additionally, CNC machines are often capable of working with a wide range of materials, including metals, plastics, and composites, allowing businesses to optimize material usage based on cost and performance requirements.
Reducing waste is not just environmentally beneficial, but it also translates to cost savings. By using only the necessary amount of material, manufacturers can lower material costs and make more efficient use of their raw resources. In high-volume production, these savings can add up quickly, making CNC machining an even more attractive option for companies looking to maximize their profitability. Furthermore, many CNC machines are equipped with features that allow them to recycle and reuse scrap material, further driving down production costs.
Lowering Setup and Tooling Costs
Tooling and setup costs can be a significant barrier for manufacturers, especially when it comes to small-batch or custom production runs. Traditional manufacturing processes often require a new set of tools and fixtures for each new job, which can be costly and time-consuming. With CNC machining processes, however, the setup process is much simpler and more cost-effective. CNC machines use digital programs, meaning they can switch between tasks without the need for major adjustments to the tools and equipment.
Additionally, once a CNC machine is set up for a specific task, it can produce consistent results without the need for frequent recalibrations. This consistency reduces the need for re-tooling and re-setting machines between runs, further lowering production costs. In industries that rely on frequent changes in product design or custom orders, the flexibility and efficiency of CNC machining offer substantial savings over traditional methods that require more complex tooling and setup adjustments for each job.
Enhancing Product Quality and Reducing Rework
Quality control is a critical aspect of any manufacturing process, and CNC machining processes provide significant advantages in this area. The high precision of CNC machines ensures that each part produced meets the exact specifications required, reducing the likelihood of defects or errors. As a result, businesses experience fewer instances of rework or scrapping of parts, both of which can drive up costs.
By minimizing defects and ensuring that parts are produced to the highest standards, CNC machining helps businesses maintain a consistent level of quality. This can lead to fewer customer complaints, higher satisfaction, and reduced warranty claims, all of which have a direct impact on a companyโs bottom line. The ability to produce parts with consistent accuracy also reduces the need for costly quality checks and inspections, further contributing to cost savings over time.
Conclusion
The use of CNC machining processes offers businesses numerous advantages, particularly when it comes to cost reduction and efficiency. From lowering labor costs and minimizing material waste to reducing setup times and enhancing product quality, CNC machining can help companies achieve significant savings across the production process. As industries continue to evolve, the demand for precision and cost-effective solutions will only grow, making CNC machining an indispensable tool for businesses looking to stay competitive. By embracing these advanced manufacturing technologies, companies can streamline their operations, improve their profit margins, and deliver high-quality products at a lower cost.
Leave a Reply