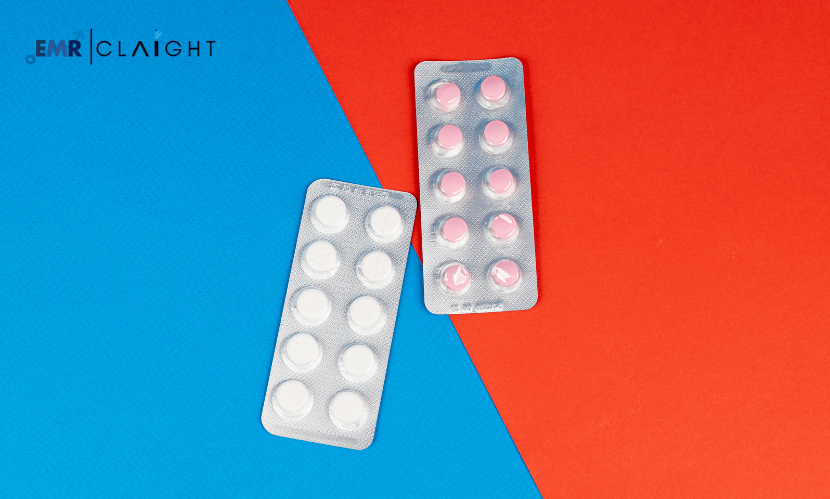
Erythromycin stearate and estolate are macrolide antibiotics widely used in the treatment of bacterial infections, including respiratory tract, skin, and soft tissue infections. Known for their broad-spectrum efficacy, these formulations are essential in the pharmaceutical industry. With growing global demand for antibiotics and the need to address antibiotic-resistant strains, establishing a manufacturing plant for erythromycin stearate and estolate offers a lucrative business opportunity. These products cater to healthcare markets worldwide, addressing critical medical needs and supporting public health initiatives.
Market Overview
The market for erythromycin stearate and estolate is expanding due to the rising prevalence of bacterial infections and the widespread use of macrolide antibiotics in healthcare. These formulations are favoured for their efficacy against a range of gram-positive and some gram-negative bacteria. Increasing awareness of antimicrobial resistance has also driven research and development, ensuring sustained relevance in the pharmaceutical market. Emerging markets with improving healthcare infrastructure further contribute to the growing demand, making it an opportune time to invest in this industry.
Get a Free Sample Report with Table of Contents@ https://www.expertmarketresearch.com/prefeasibility-reports/erythromycin-stearate-estolate-manufacturing-plant-project-report/requestsample
Manufacturing Process
The production of erythromycin stearate and estolate involves several stages to ensure high purity, stability, and adherence to pharmaceutical standards:
-
Raw Material Procurement:
Erythromycin base and other essential chemicals are sourced from reliable suppliers to maintain consistent quality. -
Chemical Synthesis:
The erythromycin base undergoes controlled chemical reactions with stearic acid (for stearate) or a salt of lauryl sulfate (for estolate) to form the desired compound. -
Crystallisation and Purification:
The crude product is purified using crystallisation techniques to remove impurities and achieve pharmaceutical-grade purity. -
Drying and Milling:
The purified compound is dried and milled into a fine powder suitable for further formulation. -
Formulation:
The active pharmaceutical ingredient (API) is formulated into tablets, capsules, or suspensions to cater to different medical needs. -
Packaging:
The final product is packaged in tamper-proof containers to maintain quality and ensure safe handling during distribution. -
Quality Control:
Rigorous testing is conducted at each stage of production to ensure compliance with regulatory and quality standards.
Key Considerations for Setting Up the Plant
- Location: Select a site with access to raw materials, skilled labour, and transportation facilities for efficient operations.
- Infrastructure: Invest in advanced reactors, filtration systems, and quality control equipment to optimise production processes.
- Compliance: Adhere to Good Manufacturing Practices (GMP) and obtain necessary certifications for pharmaceutical manufacturing.
- Workforce Training: Employ skilled personnel trained in pharmaceutical production, quality assurance, and safety protocols.
Benefits of Erythromycin Stearate/Estolate Manufacturing
- High Demand: Essential antibiotics widely prescribed for bacterial infections.
- Global Applications: Used in healthcare systems worldwide, ensuring consistent market opportunities.
- Versatile Dosage Forms: Available as tablets, capsules, and liquid suspensions, catering to various patient needs.
- Export Potential: Increasing demand in emerging markets with expanding healthcare access.
Target Audience
The primary consumers of erythromycin stearate and estolate include:
- Hospitals and Clinics: Healthcare providers prescribing antibiotics for bacterial infections.
- Retail Pharmacies: Pharmacies offering antibiotics to outpatient populations.
- Government Health Programs: Initiatives ensuring access to essential antibiotics in underserved regions.
- Pharmaceutical Distributors: Companies supplying antibiotics to healthcare facilities and retail outlets.
Challenges and Solutions
- Raw Material Costs: Fluctuations in the cost of raw materials can impact production. Establishing long-term supplier agreements ensures cost stability.
- Regulatory Compliance: Meeting stringent pharmaceutical regulations requires robust quality assurance systems and adherence to global standards.
- Market Competition: Differentiating products through superior quality, competitive pricing, and innovative formulations strengthens market positioning.
Marketing Strategies
To establish a strong presence in the erythromycin stearate/estolate market, manufacturers can adopt the following strategies:
- Collaborations: Partner with hospitals and healthcare organisations to promote the products and expand reach.
- Awareness Campaigns: Educate healthcare professionals and consumers about the benefits of macrolide antibiotics through targeted marketing efforts.
- Government Partnerships: Collaborate with public health programs to supply erythromycin products for large-scale treatment initiatives.
- Product Differentiation: Offer innovative packaging, extended shelf life, and various dosage forms to cater to diverse consumer needs.
Sustainability in Manufacturing
Sustainability is an integral part of modern pharmaceutical manufacturing. Implementing energy-efficient production processes, minimising waste, and adhering to environmental regulations can significantly reduce the environmental impact. Additionally, offering recyclable or biodegradable packaging materials enhances the sustainability profile of the product and aligns with global efforts to promote eco-friendly practices.
Future Outlook
The demand for erythromycin stearate and estolate is expected to grow as bacterial infections remain a major healthcare challenge. Innovations in formulations, such as extended-release versions or combination therapies, will further enhance their market potential. By focusing on quality, sustainability, and customer engagement, manufacturers can secure a competitive edge in this dynamic and essential pharmaceutical market. Establishing a manufacturing plant for erythromycin stearate and estolate offers an excellent opportunity to address global healthcare needs and contribute to improved treatment outcomes worldwide.
Leave a Reply