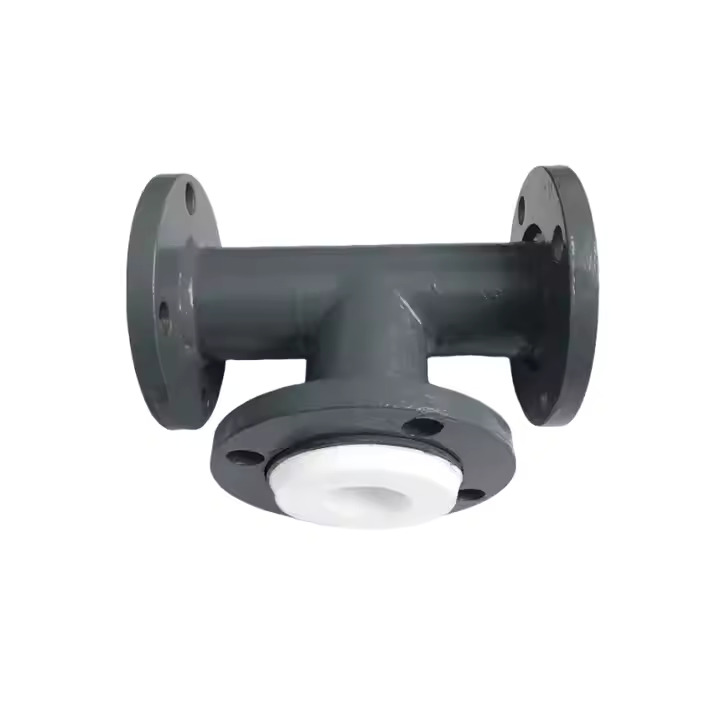
In industrial applications, durability, safety, and efficiency are of utmost importance. One method that provides long-lasting protection to equipment and machinery is rubber lining. It’s an essential process used across various industries to prevent wear, corrosion, and chemical damage. In this post, we’ll explore what rubber lining is, its benefits, and how it’s applied across multiple sectors.
What is Rubber Lining?
Rubber lining is the process of applying a layer of rubber or elastomer material to the interior surfaces of machinery and equipment. The primary purpose is to safeguard against damage caused by chemicals, abrasion, corrosion, and temperature fluctuations. Rubber linings are typically applied to tanks, pipes, pumps, and other equipment exposed to harsh environments. This process involves bonding a rubber sheet or material to a substrate (often metal or concrete) to create a protective barrier.
The rubber lining can come in various types, such as natural rubber, neoprene, nitrile rubber, and more. Each type of rubber is chosen based on its chemical resistance, temperature tolerance, and the specific requirements of the industry in question.
Key Benefits of Rubber Lining
1. Corrosion Protection
One of the most significant benefits of rubber lining is its ability to protect surfaces from corrosion. In industries like chemical processing and mining, where equipment is often exposed to corrosive substances, rubber lining acts as an effective barrier. It prevents direct contact between corrosive chemicals and the material of the equipment, thus extending the lifespan of tanks, pipes, and other machinery.
2. Resistance to Abrasion
Rubber linings are highly resistant to abrasion, which makes them ideal for industries like mining, where equipment comes in contact with abrasive materials like gravel, sand, or slurry. The durability of the rubber lining minimizes wear and tear, reducing the frequency of maintenance and repairs.
3. Chemical Resistance
Another important aspect of rubber lining is its ability to withstand a wide range of chemicals. Many types of rubber, such as neoprene and nitrile, offer resistance to acids, bases, solvents, and oils. This makes rubber-lined equipment suitable for applications in chemical processing, wastewater treatment, and more.
4. Temperature Tolerance
Rubber linings can withstand a broad range of temperatures, both high and low, depending on the rubber material used. This temperature tolerance ensures that equipment can continue to operate efficiently, even in extreme environmental conditions. In industries like petrochemical processing, where high temperatures are common, rubber lining offers a reliable solution for preventing damage to equipment.
5. Impact Absorption
Rubber’s inherent flexibility allows it to absorb shocks and vibrations effectively. This makes rubber lining an excellent option for protecting equipment from mechanical impacts that might otherwise cause cracks or failures in machinery. It helps maintain the integrity of industrial systems over time, reducing the risk of catastrophic breakdowns.
6. Cost-Effective
While the initial cost of applying rubber lining may be higher than other protective coatings, it proves to be cost-effective in the long run. Rubber linings reduce the need for frequent replacements or repairs and enhance the operational lifespan of machinery. This translates to lower maintenance costs and less downtime.
Applications of Rubber Lining
Rubber lining is versatile and used in many different industries. Let’s take a look at some of the most common applications:
1. Mining and Mineral Processing
In the mining industry, rubber lining plays a critical role in protecting equipment from the abrasive nature of materials like coal, sand, and gravel. Tanks, chutes, and slurry pipes often have rubber linings to protect them from the harsh wear caused by these materials. Rubber-lined equipment ensures smooth material flow, reduces friction, and extends the life of mining machinery.
2. Chemical Processing
The chemical industry relies on rubber lining to prevent corrosion caused by the exposure of tanks, pipes, and reactors to aggressive chemicals. Rubber linings, especially those made from materials like neoprene or EPDM, offer resistance to acids, alkalis, and solvents. This helps reduce the risk of leaks, failures, and contamination, ensuring safe and efficient operations.
3. Water Treatment
In water and wastewater treatment plants, rubber lining is used to protect pipelines, tanks, and other equipment from the corrosive effects of water, sludge, and chemicals used in the treatment process. Rubber linings prevent corrosion from saltwater or acidic substances, reducing the chances of equipment failures and extending service life.
4. Oil and Gas
The oil and gas industry uses rubber lining in tanks, pipes, and storage vessels that handle crude oil, natural gas, and other petroleum products. The rubber lining prevents corrosion from hydrocarbons and extends the life of equipment in these challenging environments. Additionally, rubber linings help in preventing spills and leaks, ensuring the safety of workers and the surrounding environment.
5. Food and Beverage Industry
Rubber lining is also found in the food and beverage sector. Food processing equipment like mixing tanks, piping, and conveyors are often rubber-lined to prevent contamination. Food-grade rubber linings offer excellent resistance to wear and are easy to clean, ensuring hygiene and food safety standards are maintained.
How Rubber Lining is Applied
The rubber lining process generally involves the following steps:
1. Surface Preparation
Before the rubber lining is applied, the surface of the equipment must be thoroughly cleaned and prepared. This may involve abrasive blasting, grinding, or chemical cleaning to remove rust, dirt, and other contaminants that could affect the adhesion of the rubber material.
2. Rubber Selection
The type of rubber lining chosen depends on factors like the chemicals involved, temperature ranges, and the type of mechanical stresses the equipment will endure. Each rubber material offers distinct benefits, so selecting the right one is critical for achieving optimal protection.
3. Application of Rubber
Once the surface is ready, the rubber lining is applied to the equipment using adhesives, heat, or other bonding techniques. In some cases, the rubber material is vulcanized or cured to ensure strong adhesion and durability.
4. Inspection and Testing
After the rubber lining is applied, the equipment undergoes a series of inspections to ensure the lining is properly bonded and free of defects. The lining is also tested for chemical resistance, temperature tolerance, and impact resistance.
Conclusion
Rubber lining is a vital process in ensuring the longevity and efficiency of industrial equipment. Its ability to protect against corrosion, abrasion, and chemical damage makes it an invaluable asset in sectors like mining, chemical processing, water treatment, and oil and gas. By using the right rubber lining material for each application, industries can ensure that their machinery operates smoothly, reducing maintenance costs and downtime.
For businesses looking to extend the lifespan of their equipment and reduce the risks associated with harsh environmental conditions, rubber lining offers a cost-effective and reliable solution. If you’re in need of rubber lining services, ensure you work with an experienced professional who understands the unique needs of your industry.
Leave a Reply