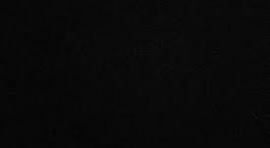
In today’s fast-paced manufacturing landscape, industries are constantly on the lookout for ways to improve efficiency, precision, and versatility in their production processes. One technology that has emerged as a game-changer in this regard is Tube Laser Cutting. This innovative method is transforming how metal components are processed and has become a cornerstone in several industries, from automotive and aerospace to furniture and medical equipment. But what exactly makes tube laser cutting so revolutionary, and how can businesses leverage its advantages to stay ahead of the competition?
What Is Tube Laser Cutting?
At its core, Tube Laser Cutting is a process that uses a high-powered laser to cut through various types of metal pipes or tubes. Unlike traditional cutting methods, laser cutting offers several advantages, including greater precision, cleaner edges, and faster processing times. The laser is focused on the material, melting or vaporizing the metal at the point of contact, which allows for intricate designs and complex shapes to be cut with ease.
This method is particularly beneficial when working with hollow or cylindrical materials that need to be shaped into specific forms, such as structural components, pipes, and frames used in a variety of applications.
Key Benefits of Tube Laser Cutting
1. Precision and Accuracy
One of the standout advantages of tube laser cutting is the incredible precision it offers. The process is computer-controlled, which ensures that every cut is made with exceptional accuracy. This level of precision is crucial for industries that require tight tolerances and detailed designs, such as automotive manufacturing or medical equipment production.
Laser cutting machines can achieve very fine details, even in intricate patterns and shapes, without the need for additional finishing processes. This leads to a significant reduction in waste and the need for rework, ultimately saving time and money.
2. Speed and Efficiency
Another reason why tube laser cutting has gained traction in modern manufacturing is its speed. Unlike traditional cutting methods that may require multiple steps or machines, tube laser cutting is a one-step process. This means that manufacturers can achieve quicker turnaround times, even on complex projects. The ability to cut through a range of materials rapidly also enhances overall production efficiency.
Moreover, the high-powered lasers used in tube cutting can handle various metals, including stainless steel, carbon steel, and aluminum, allowing for greater versatility and efficiency in production runs.
3. Minimal Material Waste
In traditional cutting methods, a significant amount of material may be wasted due to inaccurate cuts or the need for additional processes like deburring. Tube laser cutting minimizes this waste by using precise, clean cuts that reduce the need for rework. This means that manufacturers can achieve optimal material utilization, which not only saves on raw materials but also makes the production process more environmentally friendly.
4. Flexibility in Design
Tube laser cutting opens up new possibilities for design flexibility. Designers and engineers can push the limits of creativity without worrying about the constraints that come with traditional cutting methods. The laser can cut complex geometries, including curved and angular shapes, with ease. This allows for more innovative and unique designs in industries such as furniture production, automotive engineering, and even sports equipment manufacturing.
Whether it’s cutting a series of small holes, creating intricate patterns, or producing precise angled cuts, tube laser cutting can accommodate a wide range of designs that were previously difficult or impossible to achieve with conventional methods.
5. Cost-Effectiveness
While the initial investment in tube laser cutting technology may seem high, the long-term benefits far outweigh the costs. Because the process is highly efficient and precise, manufacturers can save money on raw materials, labor, and equipment maintenance. Additionally, the reduction in waste and the need for fewer post-processing steps means that overall production costs are significantly reduced.
Furthermore, the speed of tube laser cutting allows for faster production times, which means businesses can handle higher volumes of orders and increase their output without compromising on quality.
Industries Benefiting from Tube Laser Cutting
The versatility and efficiency of tube laser cutting have made it an essential tool across many industries. Below are just a few examples of how this technology is revolutionizing manufacturing processes in various sectors:
1. Automotive Manufacturing
In the automotive industry, precision and speed are critical. Tube laser cutting is used extensively to produce parts such as exhaust systems, frame components, and structural supports. The ability to cut through metal tubes and pipes with accuracy ensures that automotive manufacturers can meet strict quality standards while reducing the time required for production.
2. Furniture and Metalworking
For the furniture industry, tube laser cutting offers a streamlined process for crafting metal frames and parts used in everything from office furniture to home decor. The clean cuts and versatile design possibilities allow for more modern, creative designs while maintaining structural integrity. The ability to handle high volumes and intricate designs is a major asset to metalworking companies that specialize in custom pieces.
3. Medical Equipment Manufacturing
In the medical field, especially for devices that require high precision, tube laser cutting has become indispensable. Surgical instruments, diagnostic devices, and other critical components benefit from the extreme accuracy and smooth finishes that laser cutting provides. This ensures that products meet the high standards required for patient safety and medical efficacy.
4. Sports Equipment
Sports equipment manufacturers rely on tube laser cutting to produce lightweight yet durable components. Whether it’s for bicycles, ski poles, or custom sporting gear, laser cutting allows for the precise and clean cutting of metal tubes, ensuring that the equipment is both functional and high-performing.
5. Electronics and Aerospace
Tube laser cutting plays an essential role in producing components for the electronics and aerospace industries, where precision is paramount. Thin-walled tubes used in electronics, as well as parts for aircraft and spacecraft, require the utmost care in their fabrication. Laser cutting ensures these components meet the rigorous quality standards required in these high-stakes sectors.
The Future of Tube Laser Cutting
As technology continues to evolve, the capabilities of tube laser cutting will only improve. We are already seeing advancements in machine technology, including five-axis laser cutters and more energy-efficient laser sources. These innovations promise even faster cutting speeds, increased material compatibility, and greater precision than ever before.
Moreover, with the ongoing push for sustainable manufacturing practices, tube laser cutting offers a greener solution by reducing waste and energy consumption. Manufacturers that embrace these cutting-edge technologies will be better positioned to meet the growing demand for eco-friendly, high-quality products.
Conclusion: A Game-Changer for Modern Manufacturing
Tube laser cutting is revolutionizing industries across the globe by offering precise, efficient, and cost-effective solutions for metal tube and pipe fabrication. From automotive and aerospace to medical equipment and furniture, the benefits of tube laser cutting are far-reaching. As technology advances, this cutting-edge method will continue to push the boundaries of what is possible in manufacturing.
For businesses looking to stay ahead of the curve, embracing tube laser cutting could be the key to gaining a competitive edge. Whether you’re aiming to improve your production efficiency, reduce waste, or create more innovative designs, this technology holds the potential to transform your manufacturing processes for the better.
Leave a Reply