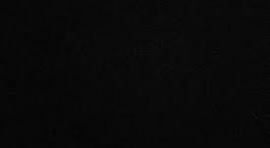
Tension sensors, also known as load cells or force sensors, are integral to various industries that rely on accurate force measurements. From manufacturing and automotive to aerospace and medical applications, these devices ensure precise control, performance, and safety. In this article, we will explore the fundamental role of Tension Sensor, their applications, and how they contribute to the efficiency and reliability of modern systems.
What Are Tension Sensors?
At their core, tension sensors are devices designed to measure the force or load exerted on an object, specifically in tension (pulling force). These sensors are often part of a larger system that helps monitor, control, and optimize processes that require the measurement of mechanical forces.
Tension sensors are typically used to convert mechanical forces into electrical signals. This transformation allows for highly accurate readings of the applied force, which can be displayed or processed by a connected system. While they come in many forms, the most common tension sensors are based on strain gauge technology, which changes resistance in response to strain caused by an applied force.
How Do Tension Sensors Work?
Tension sensors utilize the principle of strain gauges, which are bonded to a structure that deforms under an applied load. As the tension or pulling force is applied, the material deforms slightly, causing the strain gauges to stretch or compress. This change in shape alters the electrical resistance of the strain gauges, which is then measured and converted into a signal that corresponds to the magnitude of the applied force.
The sensor typically consists of a metal body (the load-bearing part), with the strain gauges placed in strategic locations. When the object experiences tension, the deformation in the metal body directly affects the strain gauges, allowing the tension sensor to provide highly accurate measurements of the force.
Types of Tension Sensors
There are several different types of tension sensors, each designed for specific applications. Here are some of the most common types:
1. S-Type Tension Sensors
S-type tension sensors are one of the most versatile and widely used types. Their S-shape allows them to measure both tension and compression forces, making them highly adaptable to various measurement needs. These sensors are commonly used in applications such as material testing, load measurement, and monitoring the force exerted on machines and tools.
2. Load Cell Tension Sensors
Load cells are a specific type of tension sensor designed to measure force by converting mechanical stress into electrical signals. There are different types of load cells, including hydraulic, pneumatic, and strain gauge load cells. Among these, the strain gauge-based load cells are the most commonly used for tension measurements due to their high accuracy and reliability.
3. Rotary Tension Sensors
Rotary tension sensors are used for measuring forces in rotational or angular movements. These sensors are often used in applications where the object is moving or rotating, such as in industrial machines, winches, or cable monitoring systems.
4. Capacitive Tension Sensors
Capacitive tension sensors use changes in capacitance to measure the applied force. These sensors are often used in situations where precise measurements are needed for small forces or in environments where other types of sensors may be compromised due to extreme conditions like high temperatures or vibrations.
Applications of Tension Sensors
Tension sensors have a broad range of applications in industries where accurate force measurement is critical. Let’s explore some of the key sectors that rely on these sensors.
1. Manufacturing and Automation
In manufacturing, tension sensors are essential for quality control, process optimization, and machinery maintenance. For example, in production lines, they monitor the force applied during operations such as stamping, pressing, or assembly. This helps ensure that the machines are operating at optimal force levels, preventing overloading or underperformance.
Tension sensors are also used in automated systems for precise control over material handling, ensuring that materials are moved or processed without damage. In conveyor belts, for instance, they help monitor the tension in the belt, ensuring that the load is evenly distributed and preventing belt slippage.
2. Automotive Industry
The automotive industry uses tension sensors for testing the strength and durability of materials used in vehicles. They help ensure that components, such as cables, springs, and structural elements, can withstand the forces they will experience during normal operation. Additionally, tension sensors are used in the calibration and maintenance of car suspension systems, ensuring that they operate efficiently and safely.
3. Aerospace
In aerospace applications, tension sensors play a vital role in testing materials and components that must meet strict safety standards. From aircraft structural testing to cable force monitoring in aircraft control systems, these sensors help ensure that the forces involved in flight are accurately measured and monitored.
4. Medical Devices
Tension sensors are also used in medical applications, particularly in prosthetics and orthopedic devices. They help measure the force exerted by or on medical components, ensuring they provide the necessary support and function as intended. In medical research, tension sensors are used in testing materials for implants or other medical devices, ensuring their strength and durability before they are used in patients.
5. Marine and Oil & Gas
In industries like marine and oil and gas, tension sensors are crucial for monitoring the forces exerted on equipment in harsh environments. For instance, in offshore drilling rigs, tension sensors are used to monitor the load on cables and winches, ensuring they do not exceed their maximum capacity. These sensors help prevent accidents and ensure the safety and reliability of operations.
Key Features to Look for in Tension Sensors
When choosing a tension sensor for a specific application, several key features should be considered:
1. Wide Measuring Range
A tension sensor with a wide measuring range can handle a broad spectrum of forces, making it suitable for applications that require both low and high force measurements.
2. High-Level Ingress Protection
In environments where the sensor may be exposed to dust, moisture, or other contaminants, high ingress protection (IP) ratings are essential. Sensors with high IP ratings ensure reliable performance, even in challenging conditions.
3. Variety of Output Formats
Tension sensors should offer various output formats (analog, digital, etc.) to ensure compatibility with the monitoring and control systems in use. Some sensors also come with built-in amplifiers to enhance signal processing.
4. Customization Options
Customization is key for ensuring that the sensor meets the specific needs of a given application. Sensors that can be tailored in terms of size, shape, and materials provide greater flexibility and adaptability.
Conclusion: The Future of Tension Sensors
Tension sensors are indispensable in ensuring the precision and safety of countless industrial applications. As technology continues to advance, these sensors will become even more accurate, versatile, and reliable. The ongoing trend toward automation and digitalization will only increase the demand for these crucial devices, as industries seek smarter ways to monitor and control their processes.
In the near future, tension sensors may evolve to include additional capabilities, such as wireless data transmission, real-time monitoring, and advanced data analytics. These advancements will open up new opportunities for industries to optimize their operations, improve safety standards, and enhance product quality.
As businesses continue to explore the potential of tension sensors, the possibilities for innovation and efficiency are limitless. Whether you’re in manufacturing, aerospace, automotive, or medical sectors, the role of tension sensors in improving processes and outcomes cannot be overstated. As technology advances, it will be exciting to see how these sensors evolve and transform industries worldwide.
Leave a Reply